まるでひとつの街のようだ・・・と感じたビッグスケール
まずはじめに、筆者は2023年4月にモーターマガジン社に新卒入社した新入社員。もちろんクルマが大好きで念願叶い編集部に入ったわけだが、クルマが作られている場所、すなわち工場ラインを実際に見たのは今回が人生で初めてだった。
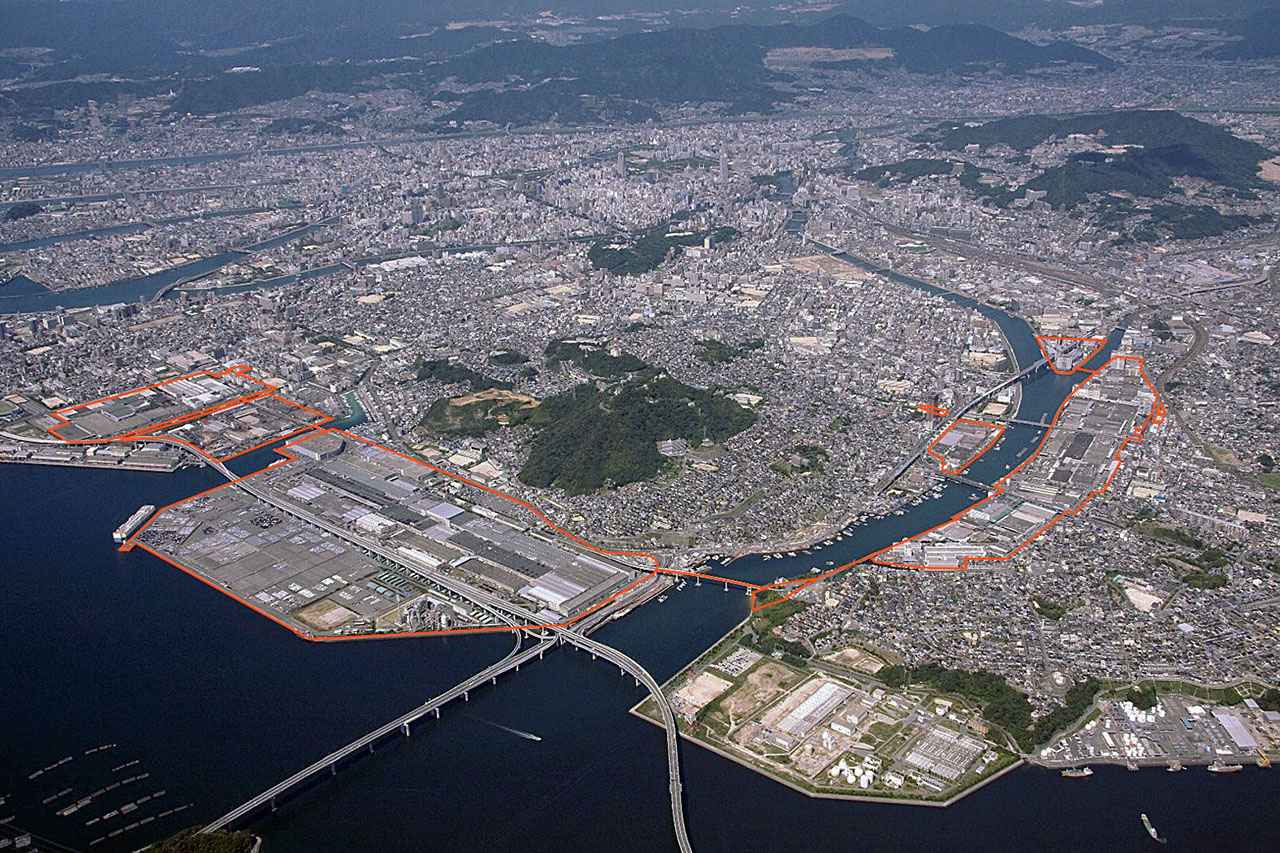
マツダ本社工場のエリアは写真赤枠の中。非常に大きな敷地の中には、自社用の火力発電所も設備される。(写真:マツダ株式会社)
そしてマツダの工場見学に参加できると聞いた時、初めて“クルマが誕生する瞬間”を見ることができるとワクワクした。けれど実際に見学した後に一番印象に残ったことは、実際に見たという感動以上に、マツダの思想や大事にしているコトやモノが何かをよく知ることができたという経験だった。
まずマツダ本社工場は、広島県安芸郡府中町にその名の通り本社と併設されている。マツダにとってメイン工場となる本社工場だが、その大きさはおよそ223万平方メートルで、マツダスタジアム97個分に相当する。それは、東京ドームで例えるならばおよそ47個分にあたる。巨大ともいえるこの本社工場では、ロードスター(RF含む)とCX-5/CX-8、海外向けのCX-9、そしてCX-30/MX-30といった主力車種を製造している。
工場の規模は、想像以上のものだった。マツダ本社工場の敷地内には大きな橋があり、一見すると一般道路にいると思い込みそうな風景だった。また自社の火力発電所も備えられるなど、ひとつの街のような巨大さに驚いた。
意外にもハンドメイドなマツダ車には「想い」がつまっている
はじめに見学したのは、MX-30のEVモデルならびにロータリーEVで使用されるバッテリーの取り付け工程。土台の上にバッテリーセルという、例えるならば巨大な乾電池のようなものを、各車両に合わせて必要な数だけ載せていくというもの。
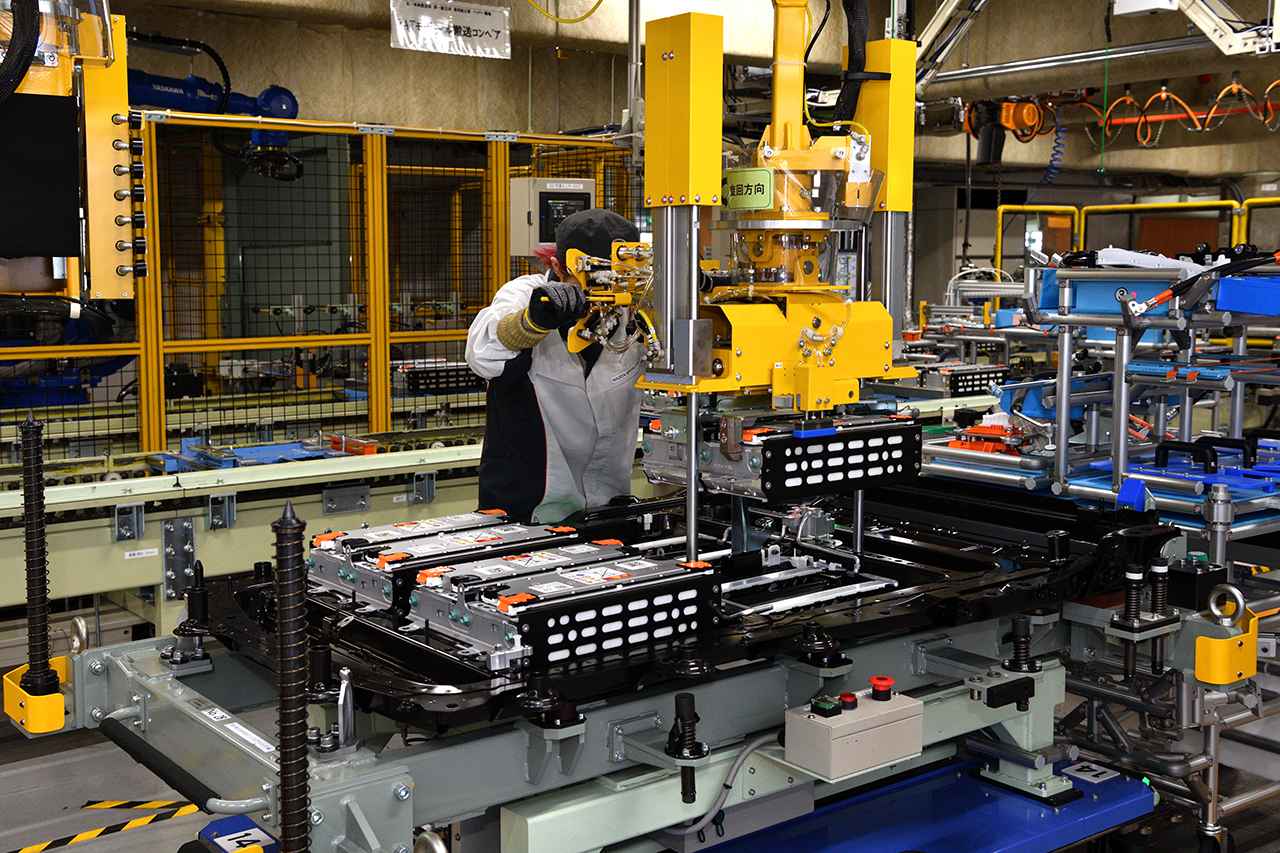
バッテリーセルはEVモデルで16個、ロータリーEVで8個搭載する。機械は女性でも扱える操作性の良いものだ。(写真:マツダ株式会社)
この載せてゆく工程は、人間が機械を駆使しながら取り付けを行っていた。無知な私は、こういった工程ではすべてロボットを使って生産していると思っていたため、その事実に驚いた。しかも、正確に取り付けられているかどうかを教えてくれるセンサーが機械に搭載されているため、人が操作をしてもミスなく安心して作業を行えるというから凄い。
このバッテリーは取り付け後、出荷前に備えて充電をする。そこで驚いたのが、この充電するための電力は、工場上に設置される太陽光パネルから生み出されているというのだ。こういったマツダの、環境に対する姿勢や、人やモノを想う気持ちが見学した各所で現れていた。
ボディにエンジンやバッテリーが搭載される瞬間を見た
続いて見学したのは、車両組み立ての様子。ここは出荷前の最終工程となり、塗装まで終えたボディと、組み立てが終了したエンジンやバッテリーを最後に合わせている場所。ここにも、マツダらしい製造への知恵や想いが詰まっていた。

写真のクルマはMX-30 ロータリーEV。写真下のオレンジ色の土台に乗せられて、バッテリーと燃料タンクが自動でここまでやってくる。(写真:マツダ株式会社)
まずこの車両組み立ても有人作業によって行われる。そしてマツダの生産工程は、フレキシブル生産を実現している。これは工場ラインにおいて、車両の組み立てに変動対応した工程や設備を設定し、さまざまな車種やパワートレーンを同じラインで生産可能にしたというもの。したがって、同じライン上でFRのロードスターからFFのMX-30、ガソリン車からEVまで組み立てができる。これこそ古い歴史を持つ広島本社工場で、車種が増えた今も生産を続けるための“知恵”といえる
それを聞くと、組み立てる“人”はさぞ大変だろうなと思ってしまうが、ここにもマツダの人想いなアイデアがあった。組み立てる作業員は次々と流れてくるランダムな車種に対応するべく、当然知識や工程を理解しなければならないのだが、必要な部品などはすべて機械が手元まで運んできてくれる。例えばMX-30に搭載されるバッテリーは、太陽光での充電後に、ロボットが直接組み立てを行う作業員のもとまで運んできてくれるのだ。もちろん、該当車種が流れてくるタイミングに合わせてやってくる。
これを見た時、人想いなアイデアだと思ったのと同時に、機械と人の連携プレーがあってこそ、フレキシブル生産が可能なのだと感じた。と、感動している一方で別の機械が今度はロードスターのエンジンを用意して待っている……といった具合である。非常に興味深かった。