「ものづくり革新2.0」を掲げるマツダを支える生産拠点のひとつが山口県にある防府工場です。今回はこの工場を見学し、そこで見た生産効率を高める数々の努力をご紹介します。
パーツを載せた台車が自律的に動く姿はまさにSF映画の未来の工場
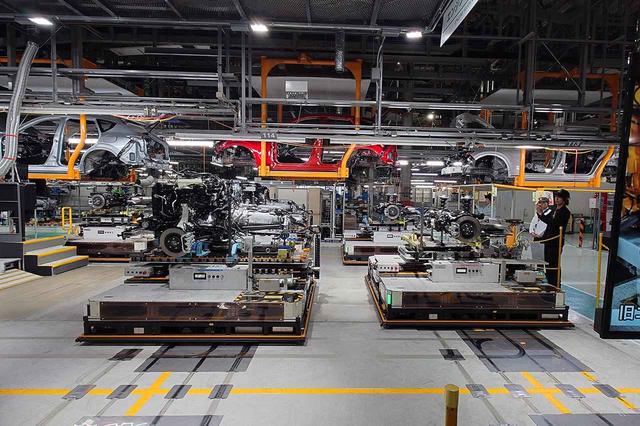
AGVは床面のマークを読むと同時に他のAGVとの距離をレーザーで計測、自律的かつフレキシブルに移動する。
マーキングされた平坦な床面を自律的に動くAGVがパワーユニットとリアの足まわりを運搬。組み付け工程では、AGVが取り付ける車種(見学したラインではCX-60、CX-80などを混流生産)を識別して位置を調整、取り付ける様子は、これまでに見てきた工場とは明らかに異なる光景です。
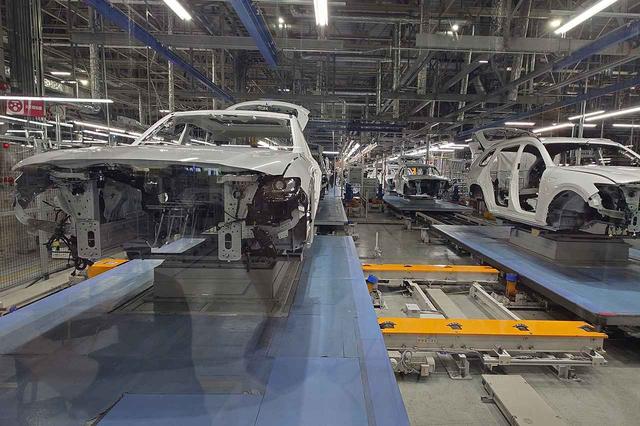
床面に設置した台車でボディを運搬する「トラバース台車ライン」。大掛かりな工事なしにラインを構築可能。
また、床面を掘るなど大掛かりな工事をせずに設置できるため、ラインの移設や増設がしやすい車体運搬システム「トラバース台車ライン」も導入されています。
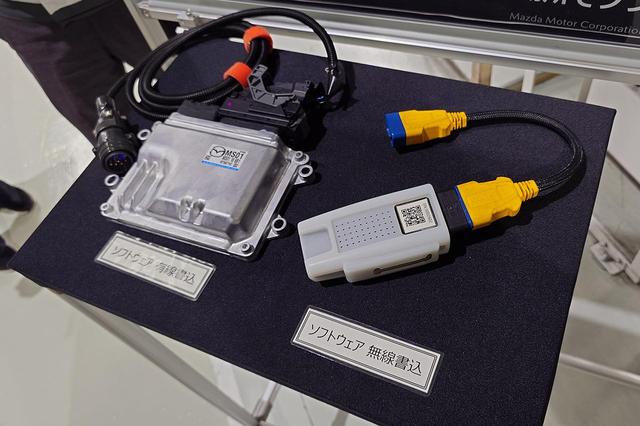
無線通信によりソフトウェアを書き込む「ファクトリーOTA」は、端末を車体のOBD2コネクタに繋いで使う。
もうひとつ触れておきたいのが、製造中の車体をライン上で動かしながらソフトウェアのインストールを行える「ファクトリーOTA」を導入です。ワイヤレスのこの機器を使うことで製造ラインで車体の組み上げしながらソフトウェアのインストールを進められるようになりました。こういった工夫に新しさを感じました。