「ものづくり革新2.0」を掲げるマツダを支える生産拠点のひとつが山口県にある防府工場です。今回はこの工場を見学し、そこで見た生産効率を高める数々の努力をご紹介します。
マツダが取り組む「ものづくり革新」に基づき効率的な生産を実現
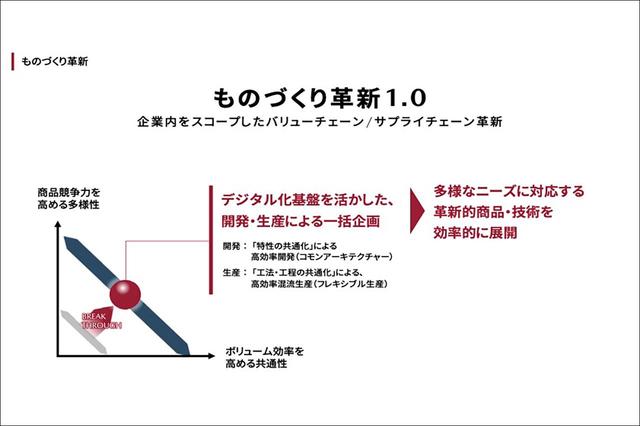
「ものづくり革新1.0」のイメージ図。初代CX-5など第6世代商品群の生産時にはほぼ達成していた。
マツダは2006年から「マツダものづくり革新1.0」という取り組みを始めました。具体的にはデジタル化基盤を活かした開発・生産による一括企画を軸に、多様なニーズに対応する技術を用いて商品を効率的に提供するというものです。その実現の手段のひとつとして、1本の製造ラインでさまざまな車種を作る混流生産を実現。工程数を4割も削減することに成功しています。
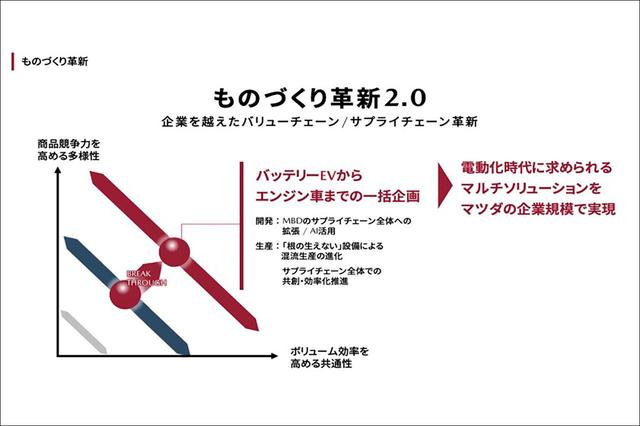
こちらは「ものづくり革新2.0」のイメージ図。パワートレーンの多様化などへの対応も目指している。
2015年には「マツダものづくり革新2.0」に移行。「1.0」で築いた単一車種だけではなくさまざまな車種をひとつのラインで組み立てられる混流生産ラインに、マツダなりの工夫を採り入れてより柔軟性を高め、MHEVを含むエンジン車、PHEV、BEVなど、さまざまなパワーユニットを搭載したモデルを1本の生産ラインで作れるようにしました。

今回見学したのは「H2工場」にあるCX-60をはじめとするFRベースのラージ商品群の生産ライン。
今回はマツダ防府工場 西浦地区 第2(H2)工場でいくつかの乗用車の組み立て工程を見学させてもらいましたが、そこではAGV(Automatic Guided Vehicle=無人搬送車)が大きな役割を担っていました。