※タイトル写真はAGVに乗せられて移動する、足まわり搭載前のGRヤリス。
GRブランドだからこそ、重要視される性能を高めるため
ではなぜ一般的なライン生産ではないのか。上述した「非効率的」ということも理由のひとつだが、複数のモデルの生産台数を需要と供給に合わせて調整しやすいこと、大幅改良や仕様変更にフレキシブルに対応できることなどが挙げられている。そしてもうひとつが、ボディをより高精度に仕上げることだ。
標準モデルの生産と異なる部分は多くあるが、興味深いのはボディの組み立てや溶接、足まわり組み付けを行なったあとに実施される検査回数の多さであり、その中でもボディ精度検査はとくにGRファクトリーならではのこだわりがあるという。
サスペンションやアーム類など足まわり部品の取り付け穴の位置を0.1mm単位で計測、部品の計測値も集約してデータ解析。互いの微妙なズレを補完して設計どおりになる組み合わせを自動選択するシステムになっている。組み合わせの数は、実に1万通りにも及ぶという。
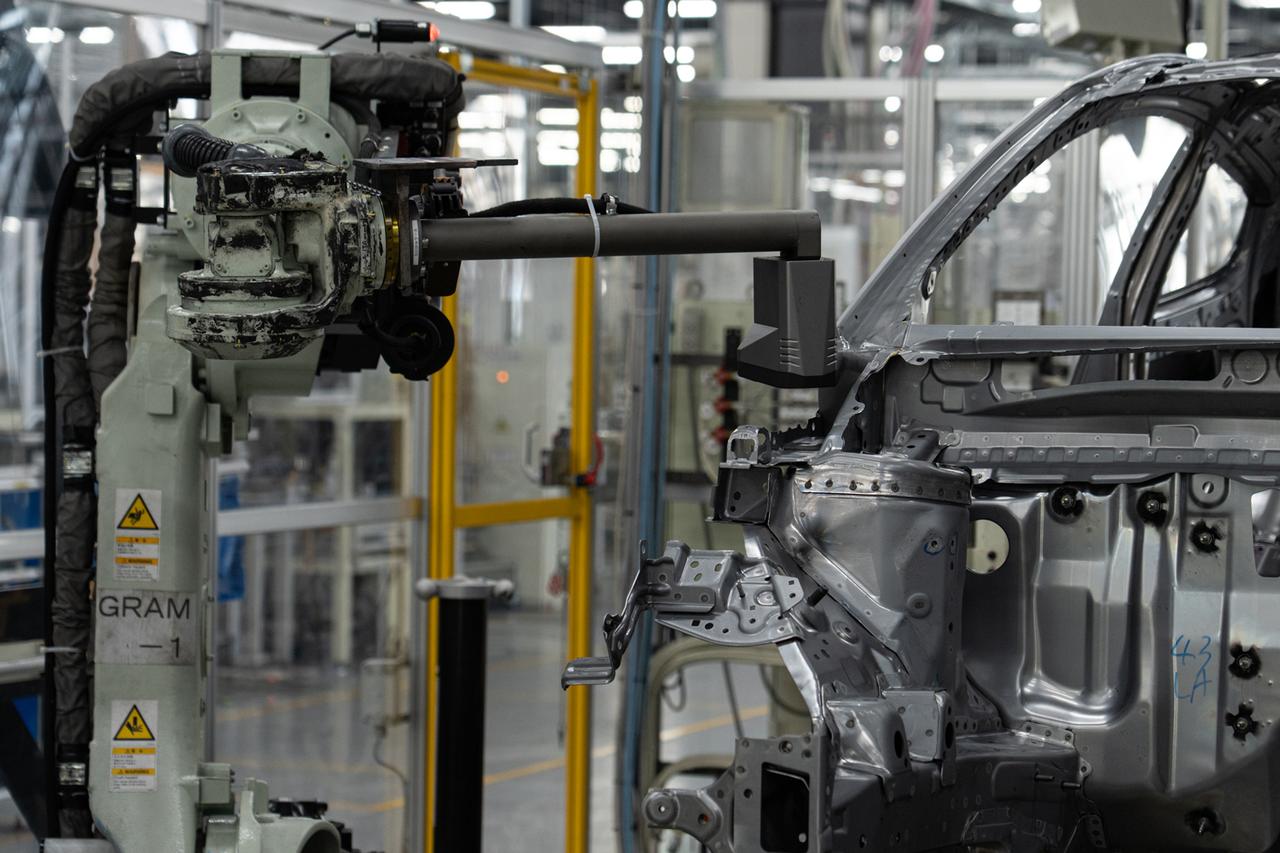
アーム先端に取り付けられたセンサーでボディ精度の3次元検査が行われ、足まわり取り付け穴の誤差を測定する。
このほかにも、足まわりのセットアップ精度を高める工程はいくつもある。一般的に足まわりの組み立ては全工程の中盤に行われるが、GRファクトリーでは最後に行うことでズレを抑制、アライメント調整の測定&調整の回数を増やしている。モータースポーツ車両で最重要とも言われる足まわりを操作に対して正確に動くように、そして高剛性で、スペックどおりの性能を引き出すために工数も時間もかけているのだ。
ちなみに、この記事を制作しているちょうど今、こうしたこだわりを公開するGRファクトリー見学ツアーが、GRヤリスとGRカローラのオーナー向けに開催されている。クルマの購入検討からサポートを行う「マイトヨタ」の登録オーナーであれば申し込みできるという。参加人数の枠に限りはあるが、気になるオーナーはアカウント登録から始めてみてはどうだろうか。